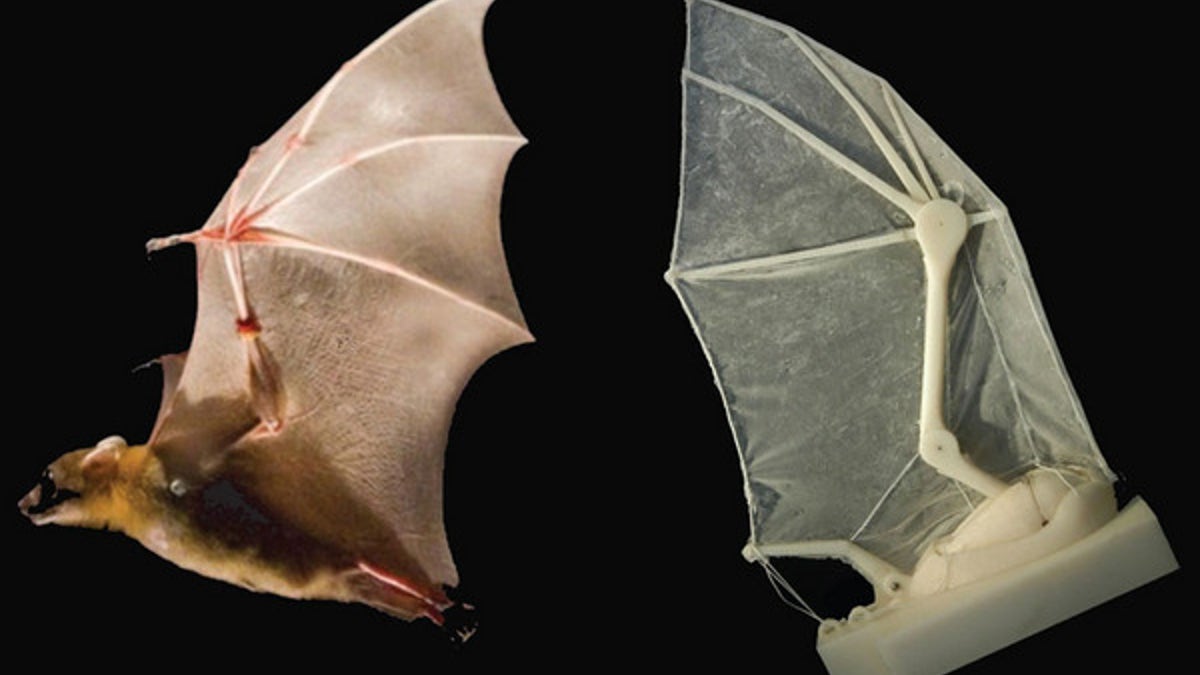
By building a robotic bat wing, scientists have uncovered flight secrets of real bats: the function of ligaments, the elasticity of skin, the structural support of musculature, skeletal flexibility, upstroke, downstroke. (Breuer and Swartz Labs / Brown University)
Robotic bat wings could aid in the design of novel flapping aircraft, researchers say.
Scientists built a robot that mimics the wing shape and motions of the lesser dog-faced fruit bat (Cynopterus brachyotis), a medium-size bat from southeast Asia whose aerodynamics have been analyzed in depth in past studies.
"Bats are some of the most spectacular fliers out there," researcher Joseph Bahlman, a biologist and engineer at Brown University, told TechNewsDaily. "Their wing structure is very different from what you find in birds and insects. An insect has one joint at the shoulder. A bird has three wing joints at the shoulder, elbow and wrist. Bats also have several joints within each of the fingers, providing up to 25 joints in the wing, all of which allow it to change the shape of the wing dramatically, for more maneuverability and fine control over flight."
The eight-inch mechanical wing imitates bat anatomy with eight plastic bones matching proportions of the real bat. Three motors pull on tendonlike cables, which in turn tug on its seven joints. The entire rig is covered by a flexible silicone rubber skin.
[Holy Bat Trick! Biosonar Could Give Robots Night Vision]
"There's a lot of interest in bat wings when it comes to building micro air vehicles, toward building small flying robots that can be sent into places that are either too small or not safe for people," Bahlman said. "There are lots of places one would want a slow and maneuverable camera."
The robot is designed to flap in a wind tunnel while sensors record the aerodynamic forces generated by the moving wing. By measuring the power output of the servo motors, scientists can evaluate the energy required to execute wing movements.
The robot does not completely match the complexity of a real bat's wing, which has 25 joints and 34 different ways it can move. Still, the artificial wing allows researchers to test flapping in a way researchers never could with live animals. For instance, scientists cannot ask bats to flap wings eight times a second instead of nine. "They don't really cooperate that way," Bahlman said.
Instead, the researchers can experiment with each aspect of the model. "We can answer questions like, 'Does increasing wing beat frequency improve lift and what's the energetic cost of doing that?'" Bahlman said.
Preliminary tests with the robot are already shedding light on how real bats fly. For instance, researchers analyzed the aerodynamic effects of wing folding — bats and some birds fold their wings back during the upstroke. Experiments with the robot wing showed that folding helps lift the animals. In flapping animals, positive lift results from the downstroke, but some of that lift is undone by the subsequent upstroke, which pushes air the other way. Trials with and without wing folding revealed folding the wing on the upstroke increased net lift by 50 percent.
The researchers made discoveries even when the robot did not work properly.
"We learned a lot about how bats work from trying to duplicate them and having things go wrong," Bahlman said.
For instance, during tests, the joint used for the mechanical bat's elbow broke repeatedly — the forces on the wing kept spreading the joint apart until it snapped. Bahlman eventually had to wrap steel cable around the joint to keep it together, a strong yet lightweight solution that resembles the ligaments around a real elbow.
Similarly, the robot wing membrane often tore at its leading edge, prompting Bahlman to reinforce that spot with elastic threads. This solution resembled the tendon and muscle that reinforces leading edges in actual bat wings, underscoring the importance of those structures.
"Building the robots taught us a lot about bats, about why they're built the way they are," Bahlman said.
Now that researchers have a working model, they plan to use it to answer many questions not possible in live bats.
"The first step involves varying the wing motion parameters to see how that affects flight performance," Bahlman said. "The next step is to start playing with the materials. We'd like to try different wing materials, different amounts of flexibility on the bones, looking to see if there are beneficial trade-offs in these material properties." Future questions involve changing the wing shape, he added.
The scientists detailed their findings Feb. 6 in the journal Bioinspiration & Biomimetics.